Electric vehicle power batteries require high power density, high energy density, long life, and environmental protection. Lithium batteries have the above advantages, so they are widely used in electric vehicles. Today, lithium batteries and their systems are managed.
This article refers to the address: http://
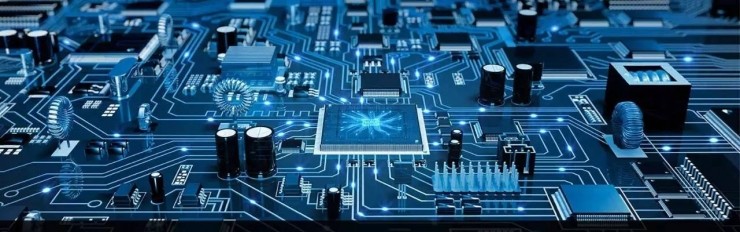
| What are the common battery types and their application requirements?
Lithium batteries for vehicles have the following:

Other types, battery discharge temperature is -20 ~ 55 °C. The charging temperature is between 0 and 45 °C. If Li4Ti5O12/LTO is used as the negative electrode material, the charging temperature can reach -30 °C, usually the lithium battery is used in the voltage range of 1.5V~4.2V (where C/NCA, C/NCM, C/LMO is 2.5V~4.2V; LTO/C/LMO is 1.5V~2.7V; C/LFP is 2.0V~3.7V).
Usually at a temperature of 90 to 120 ° C, the SEI film begins to enter the exothermic decomposition (Figure 1).
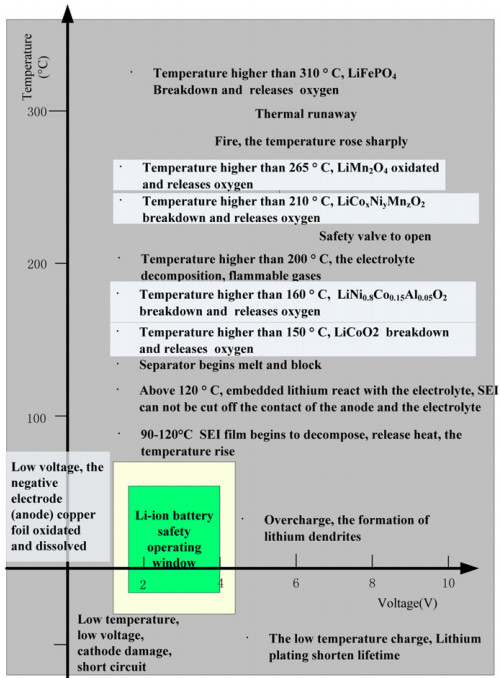
Figure 1 Battery safe working area
Some electrolytes even decompose at very low temperatures; when the temperature exceeds 120 ° C, the SEI film cannot protect the carbon negative electrode from reacting with the organic electrolyte to generate gas; when the temperature exceeds 130 ° C, the separator begins to melt and cut off the battery reaction. When the temperature is higher, the cathode material begins to decompose:
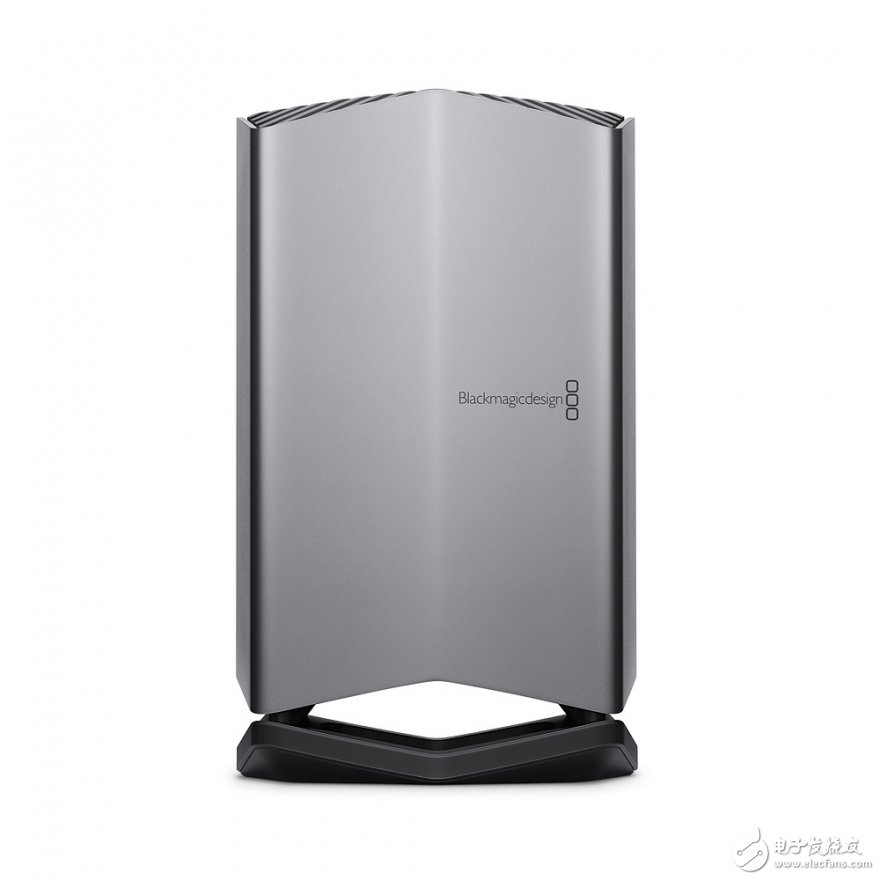
When the temperature exceeds 200 ° C, the electrolyte begins to decompose to produce a combustible gas.
The decomposed combustible gas and oxygen can undergo a violent chemical reaction and cause thermal runaway. A charging temperature of less than 0 °C causes lithium metal to deposit on the surface of the carbon negative electrode, thus reducing the cycle life of the battery. In the extreme case of low temperature, the battery negative pole can be pierced to cause a short circuit condition. If the voltage is too low or the battery is over-discharged, the phase change causes the cell lattice to collapse and affect the performance of the battery. It may even cause the anode current collecting sheet to dissolve in the electrolyte. Extreme over-discharge also leads to a reduction in electrolytes and flammable gases and thus poses a potential safety risk. High voltage and overcharge can damage the positive electrode composition and cause a large amount of heat generation. It also causes lithium metal to deposit on the surface of the negative electrode and accelerates capacity attenuation and causes internal short circuit of the battery and causes safety problems. The battery voltage starts to decompose at around 4.5V.
|Application of lithium battery in electric vehicles
At present, there are many types of power batteries used in electric vehicles. The widely used power batteries generally use LMO, LFP, NCM, and NCA as positive materials, and carbon negative materials are also used. At the same time, LTO has also been developed to improve battery life. And fast charging ability.
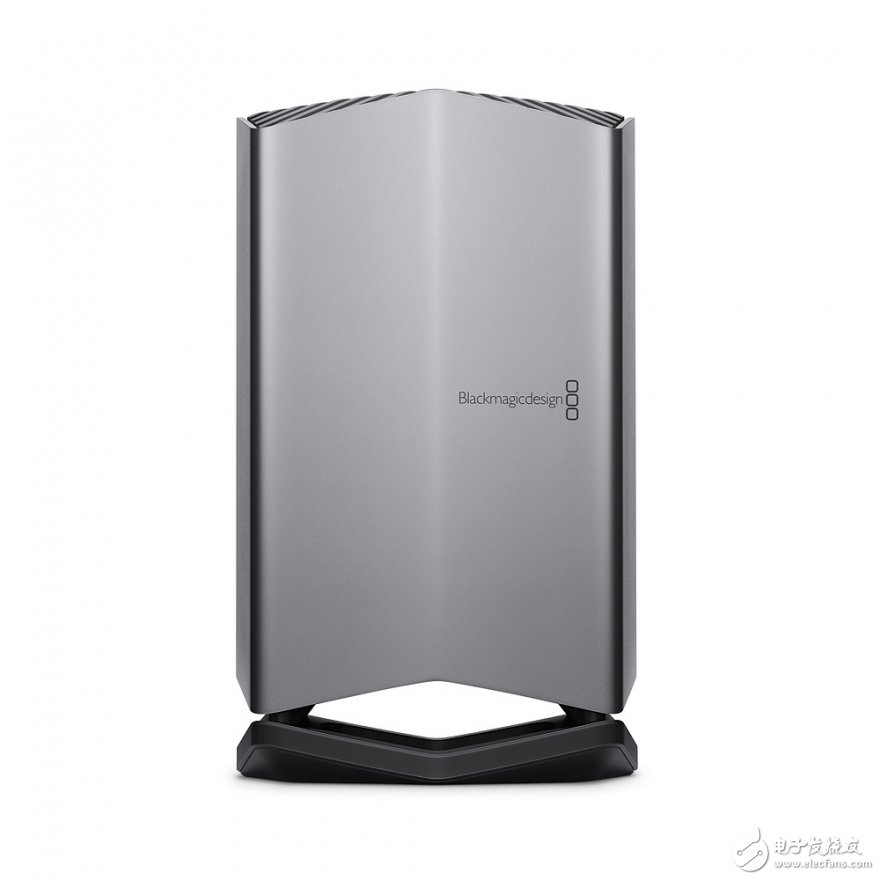
Table 1 Lithium battery application of electric vehicles
BMS function and its key technologies
| BMS function
Currently commercial batteries must have a BMS. It is more efficient to control and manage the battery through the BMS. Each battery operates within the operable range to avoid overcharging and over-discharging of the battery. The capacity of a single cell is relatively low, requiring a large number of cells to be integrated into a module, and a battery system containing multiple modules. Usually a battery system contains hundreds or even thousands of batteries. How to keep the battery working in the right range, BMS plays an important role.
The BMS function monitors battery status, establish battery status, protect battery, report data, balance, and more. The main tasks of BMS in the whole vehicle are:
1. Protect the battery cells and battery pack from damage;
2. The battery is operated within a suitable voltage and temperature range;
3. Meet the needs of the entire vehicle after keeping the battery running under the right conditions.
Of course, BMS must meet the relevant standards and regulations. The basic hardware architecture of BMS is shown in Figure 2.
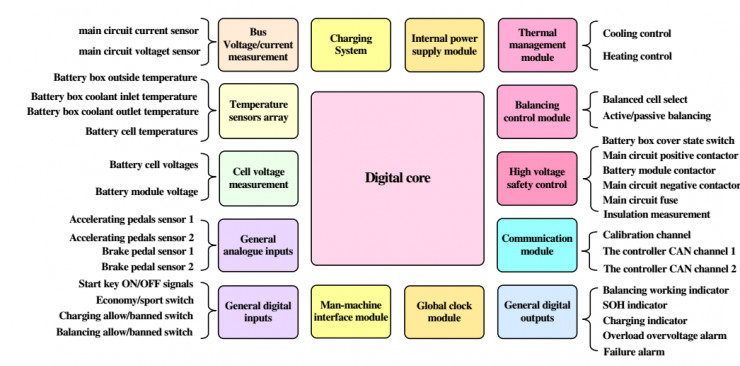
Figure 2 BMS basic hardware architecture
4, battery parameter detection: including total pressure, total current, single voltage detection, temperature detection, insulation detection, collision detection, impedance detection, smoke detection and so on.
5, battery state establishment: including SOC, SOH, SOF.
6, online diagnosis: faults include sensor failure, network failure, battery failure, battery overcharge, over discharge. Overcurrent, insulation faults, etc.
7. Battery safety protection and alarm: including temperature control system control and high voltage control. When the fault is diagnosed, the BMS reports the fault to the vehicle controller and the charger, and the high voltage is cut off to protect the battery from damage, including leakage protection.
8, charging control: BMS slow charge and fast charge control.
9. Battery consistency control: BMS collects the unit voltage information, adopts the equalization method to make the battery reach the consistency, and the battery equalization mode is dissipative and non-dissipative.
10, thermal management function: the collection temperature of each point of the battery pack, in the charging and discharging, BMS decide whether to turn on heating and cooling.
11, network functions: including online calibration and health, online program download. Usually a CAN network is used.
12. Information storage: BMS needs to store key data such as SOC, SOH, charge and discharge safety hours, fault codes, and so on.
| BMS key technology
The key technologies of BMS include accurate measurement of battery cell voltage, establishment of battery state, consistency of battery balance, and battery fault diagnosis technology.
1, single voltage measurement
Difficulties in single cell voltage measurement:
a. There are many batteries connected in series in the battery system, which requires multiple channels to collect the battery voltage. The voltage of each battery may be different, which makes the hardware circuit design difficult.
b. The measurement of the cell voltage requires high acquisition accuracy, especially the establishment of the SOC state of the battery requires high acquisition accuracy requirements.
The following takes C/LPF and C/NCM as examples: Figure 3 reflects the relationship between different open circuit voltages and SOC. It can be seen from the figure that the OCV cancellation slope of C/NCM is relatively jittery, and the maximum soc change per mv voltage. The rate is 0.4% (except 60~70%). If the measurement accuracy of the battery is 10mv, the state error established by the SOC according to the corresponding relationship of OCV will not exceed 4%. For C/NCM batteries, the measurement accuracy of the battery is less than 10mv, but the OCV curve for C/LFP is relatively flat, and the corresponding soc change rate of the voltage exceeds 4%, so the acquisition accuracy of the single voltage is required to be high. However, the accuracy of most acquisition chips can only reach about 5%. At present, the single-cell voltage acquisition is mainly performed by means of an integrated chip, and some integrated chips are listed in Table 2.
1.2 Inch Fnd Numeric Display,Indoor Fnd Numeric Display,Single Digit Fnd Numeric Display,1 Digit Fnd Numeric Display
Wuxi Ark Technology Electronic Co.,Ltd. , https://www.arkledcn.com